Safety Bulletin
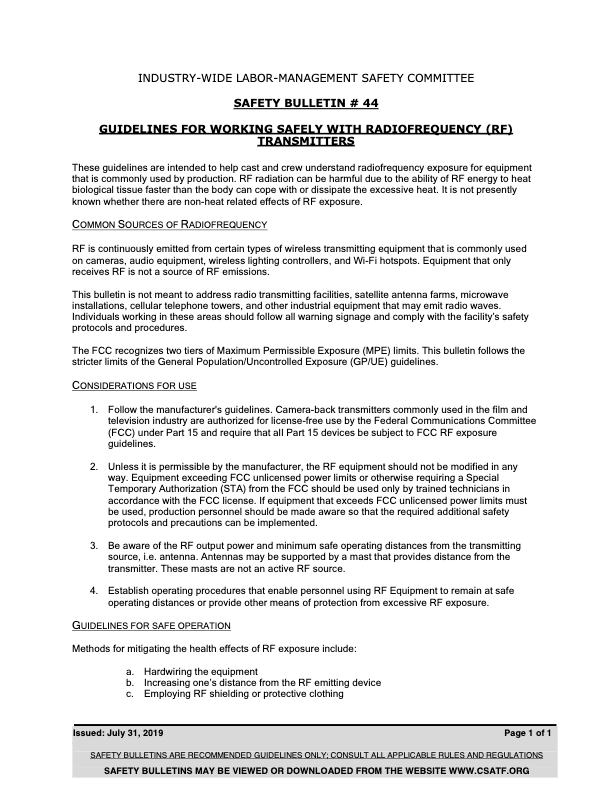
Guidelines
These guidelines are intended to help cast and crew understand radio frequency exposure for equipment that is commonly used by production. RF radiation can be harmful due to the ability of RF energy to heat biological tissue faster than the body can cope with or dissipate the excessive heat. It is not presently known whether there are non-heat related effects of RF exposure.
COMMON SOURCES OF RADIOFREQUENCY
RF is continuously emitted from certain types of wireless transmitting equipment that is commonly used on cameras, audio equipment, wireless lighting controllers, and Wi-Fi hotspots. Equipment that only receives RF is not a source of RF emissions.
This bulletin is not meant to address radio transmitting facilities, satellite antenna farms, microwave installations, cellular telephone towers, and other industrial equipment that may emit radio waves. Individuals working in these areas should follow all warning signage and comply with the facility’s safety protocols and procedures.
The FCC recognizes two tiers of Maximum Permissible Exposure (MPE) limits. This bulletin follows the stricter limits of the General Population/Uncontrolled Exposure (GP/UE) guidelines.
CONSIDERATIONS FOR USE
- Follow the manufacturer’s guidelines. Camera-back transmitters commonly used in the film and television industry are authorized for license-free use by the Federal Communications Committee (FCC) under Part 15 and require that all Part 15 devices be subject to FCC RF exposure guidelines.
- Unless it is permissible by the manufacturer, the RF equipment should not be modified in any way. Equipment exceeding FCC unlicensed power limits or otherwise requiring a Special Temporary Authorization (STA) from the FCC should be used only by trained technicians in accordance with the FCC license. If equipment that exceeds FCC unlicensed power limits must be used, production personnel should be made aware so that the required additional safety protocols and precautions can be implemented.
- Be aware of the RF output power and minimum safe operating distances from the transmitting source, i.e. antenna. Antennas may be supported by a mast that provides distance from the transmitter. These masts are not an active RF source.
- Establish operating procedures that enable personnel using RF Equipment to remain at safe operating distances or provide other means of protection from excessive RF exposure.
GUIDELINES FOR SAFE OPERATION
Methods for mitigating the health effects of RF exposure include:
- Hardwiring the equipment
- Increasing one’s distance from the RF emitting device
- Employing RF shielding or protective clothing