Safety Bulletin
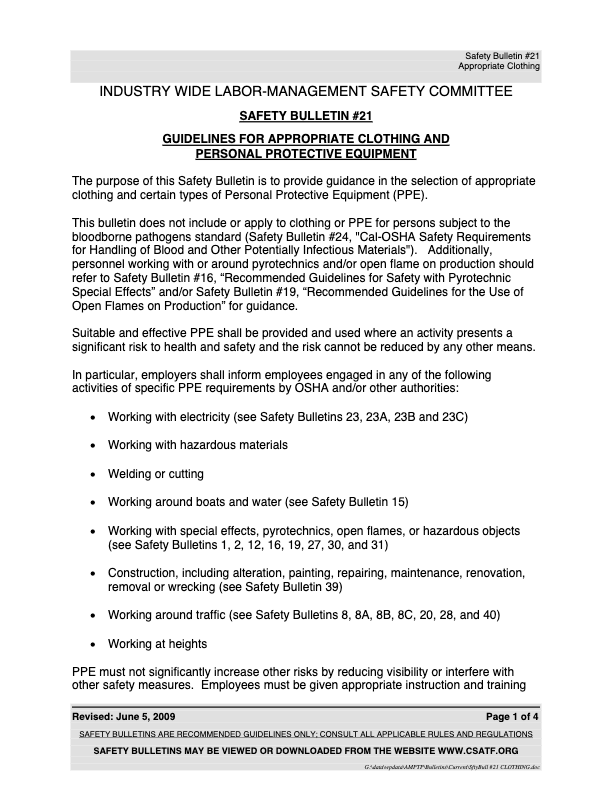
Guidelines
The purpose of this Safety Bulletin is to provide guidance in the selection of appropriate clothing and certain types of Personal Protective Equipment (PPE).
This bulletin does not include or apply to clothing or PPE for persons subject to the blood-borne pathogens standard (see Safety Bulletin: Blood and Potentially Infectious Materials). Additionally, personnel working with or around pyrotechnics and/or open flame on production should refer to Safety Bulletin: Pyrotechnic Special Effects and/or Safety Bulletin: Open Flame for guidance.
Suitable and effective PPE shall be provided and used where an activity presents a significant risk to health and safety and the risk cannot be reduced by any other means.
In particular, employers shall inform employees engaged in any of the following activities of specific PPE requirements by OSHA and/or other authorities:
- Working with electricity
- Working with hazardous materials
- Welding or cutting
- Working around boats and water
- Working with special effects, pyrotechnics, open flames, or hazardous objects
- Construction, including alteration, painting, repairing, maintenance, renovation, removal or wrecking
- Working around traffic
- Working at heights
PPE must not significantly increase other risks by reducing visibility or interfere with other safety measures. Employees must be given appropriate instruction and training on how to use any PPE issued. Once issued, PPE must be worn as required and any defects must be reported to the employer.
Clothing
- Clothing determined by the employer to be appropriate for the work being done shall be worn.
- Jewelry, loose sleeves, exposed shirt tails, neckties, lapels, loose cuffs or other loose clothing shall not be worn around machinery in which it might become entangled.
- Long hair shall be tied back when working around machinery and/or equipment with moving parts.
- Costumes should be selected and prepared in anticipation of the potential risks and hazards.
Foot Protection
- Appropriate foot protection shall be worn by employees who may be exposed to foot injuries from hot surfaces, corrosive materials, hazardous substances, falling objects, crushing or penetrating actions which may cause injuries, or who are required to work in abnormally wet or cold locations.
- Personnel working around open flame and pyrotechnic material must always wear appropriate closed-toe footwear.
Hand Protection
- Hand protection (gloves) shall be worn by employees whose work exposes them to potential injuries, such as exposure to cuts, burns, harmful physical hazards, chemical agents or electrical hazards which are encountered and capable of causing injury or impairments.
- Hand protection should not be worn if there is a danger of it becoming entangled in moving machinery.
- Hand protection should be appropriate for the type of exposure.
- Gloves should be properly discarded when they become worn, contaminated, saturated or otherwise no longer usable.
Eye and Face Protection
- Employees working where there is a risk of receiving eye injuries shall wear appropriate eye or face protection.
- Side shield protection shall also be utilized when employees are exposed to the risk of flying objects/particles/materials entering the eyes from the side.
- Suitable screens or shields isolating the hazardous exposure may be used if they provide adequate safeguarding for nearby employees.
- Specialized forms of eye protection are required for certain types of work, such as welding.
- The use of sunglasses or prescription eye glasses may not provide appropriate eye protection.
Ear Protection
- When operating or near loud equipment, amplified sound, pyrotechnics or gun fire, consideration should be given to wearing appropriate hearing protection suitable for the hazards encountered.
Head Protection
- Employees exposed to flying or falling objects and/or electric shock and burns shall be safeguarded by means of approved head protection.
- Operation of vehicles, such as motorcycles, all terrain vehicles, bicycles, etc., may require the use of a helmet. (See Safety Bulletin: Motorcycles and Safety Bulletin: Non-Camera Utility Vehicles)
Safety Vests
Federal, State and local laws require safety vests to be worn and visible when working on active public roadways.
Safety vests shall always be properly worn by employees under the following circumstances:
- During set-up, rigging, filming or striking activities performed in or near an active public roadway, unless production has obtained full closure and control of the roadway. Alternative safety considerations should be made when wardrobe requirements would prevent cast from wearing safety vests while working in or near an active public roadway without full closure and control.
- When directing traffic or responsible for lockup during partial lane closures where intermittent traffic control is used to control traffic.
Other conditions and locations may require the use of safety vests, such as railroads, subways, construction sites, airports, docks, etc.
The color of the safety vests must be either fluorescent orange-red or fluorescent yellow-green. The retro-reflective material shall be orange, yellow, white, silver, yellow- green or a fluorescent version of these colors.
Respiratory Protection
The need for respiratory protection is unique to the hazards of the workplace. Consult your employer regarding their specific respiratory protection policy.
Sanitation of PPE
- PPE shall be kept clean and in good repair.
- PPE not capable of being easily cleaned or disinfected shall be disposed of after use.
- PPE must be properly stored when not in use.